Our previous winners of the Engineering Challenges
Intermode - USA
The Intermode team has developed a small robotic autonomous delivery vehicle, which can be completely recycled at the end of its life.
The recyclability of the vehicle is further reinforced by using a single material (instead of 30 different cost optimized plastics that incur higher costs at the start) and recapturing it at end of life and making it cheaper on a total lifecycle perspective. They have designed the vehicle to be modular, such that the parts can recaptured and recycled easily at the end of life.
The team is lead by Arnold Kadiu, a mechanical engineer who has previously worked with Ford Motors as an R&D engineer.
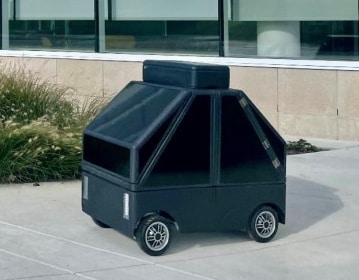
Herone - Germany
Herone produces high performance composite products
made from realigned recycled carbon fibers. Their
products are made from recycled CF, while retaining
strengths of virgin fibers. The combination of automated
textile preforming with efficient press molding – for
manufacturing of thermoplastic composite profiles
enables them to produce high performance parts from
recycled CF.
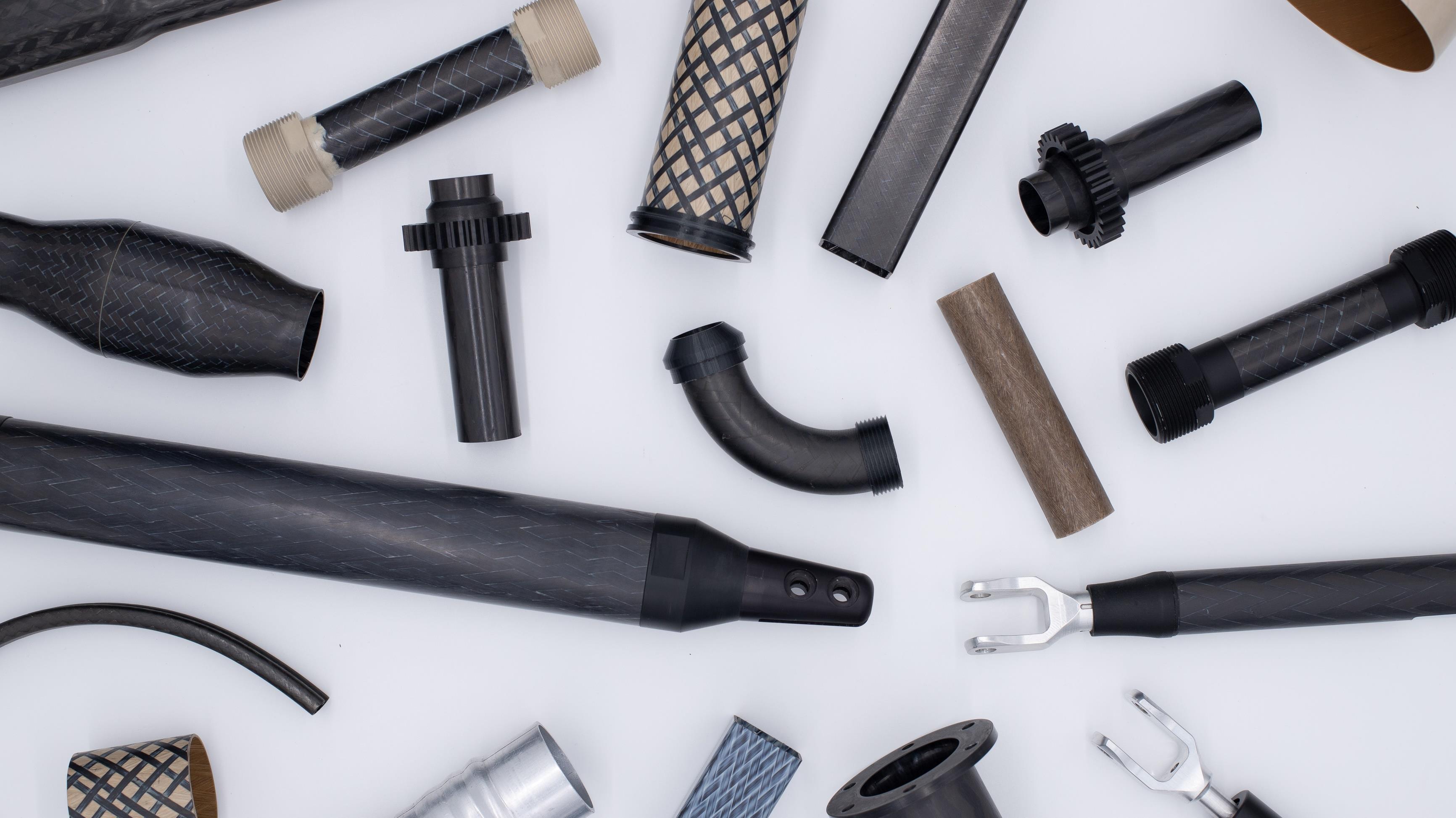
CarboScreen - Germany
CarboScreen has developed sensors for monitoring fiber and process parameters relevant for CF production in order to detect microscopic defects. A specially developed software platform based on artificial intelligence (AI) principles links the measured sensor data with process
know-how. With the software platform it is possible to recommend actions for plant operators to optimize CF production process and increase fiber quality.
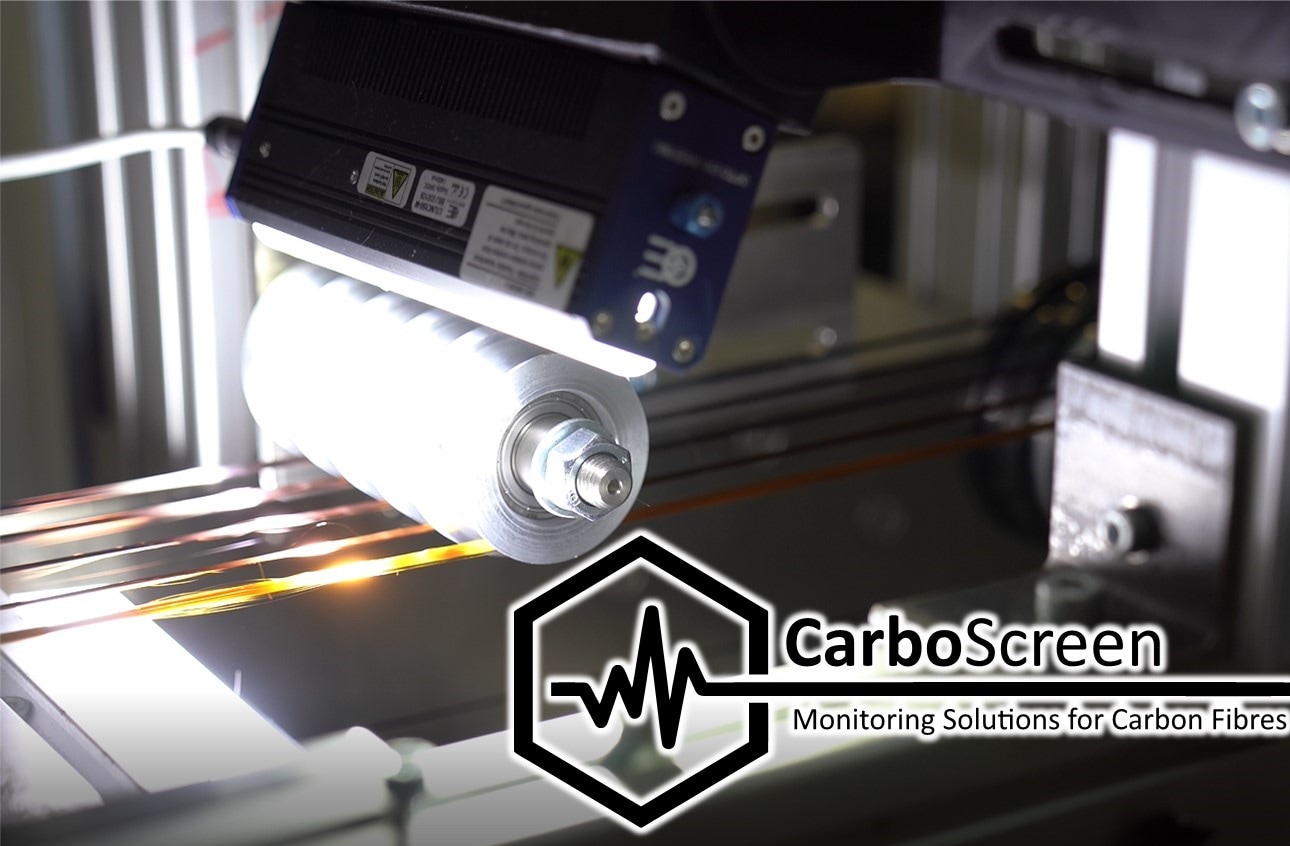
Project Unlimited - The Netherlands
The team from TU Delft is building prosthesis system that is completely tailored to the needs of the specific user. This is facilitated by building a product (prosthesis) that has a modular build-up, such that parts can be
swapped according to the evolving needs of the user.
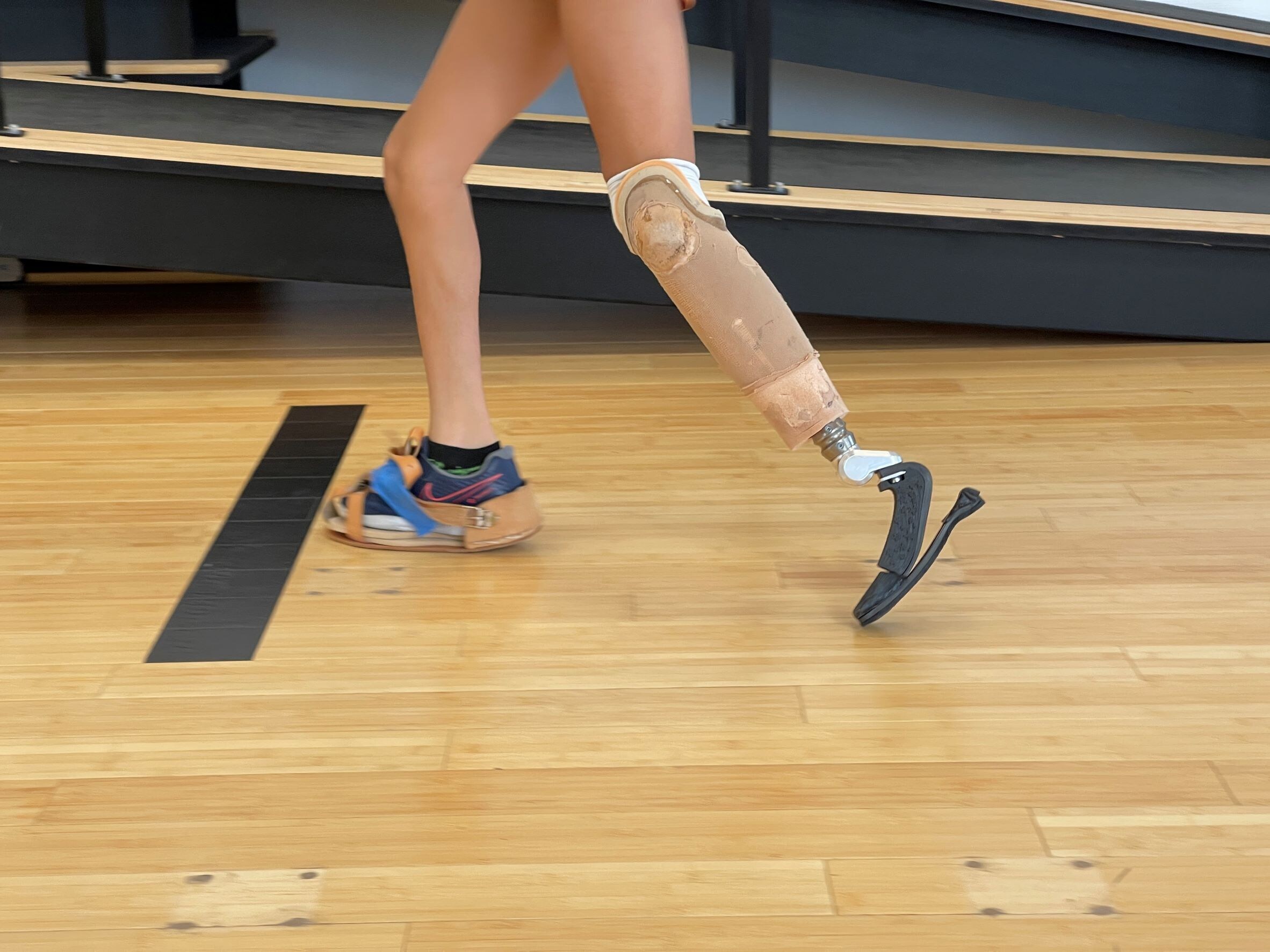
Crover Subterranean drone
Based on the 'Crover Effect' for locomotion in granular media, the CROVER robot is able to move through bulk solids and powders - i.e., environments like sand dunes, grain bulks, and chemical powders. Crover's first application is a grain Storage Management system. This helps grain storage operators like farmers, grain merchants and port operators identify critical conditions early and maintain the quality of their stock.
The winning design is a unique combination of an innovative technology with a significant positive environmental impact that addresses a key global challenge for society: food waste
Lorenzo Conti crover.tech
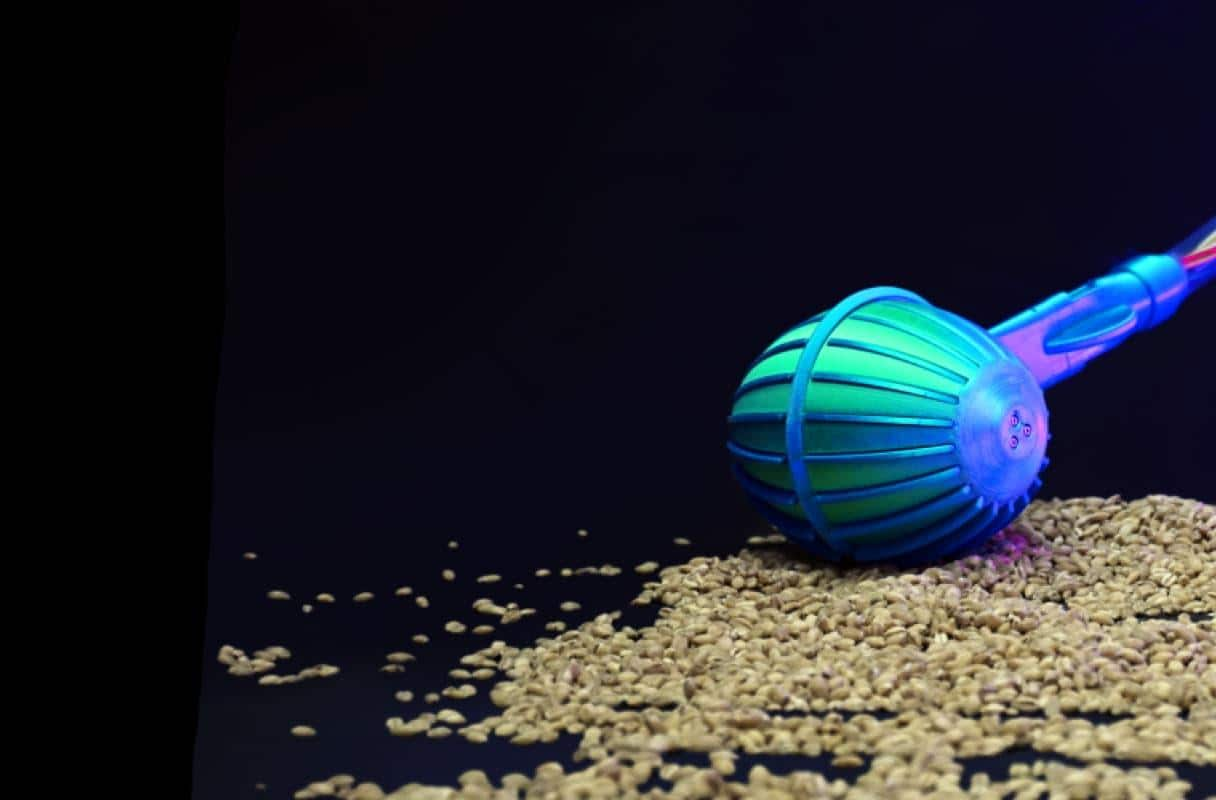
The power assisted mobility device
The team comprising two brothers Alan (a mechanical engineering student at Northeastern University) and Alberto (an industrial designer currently working at Tesla) are developing an extraordinary and life-changing product. Inspired by the story of Sophia Malthus, who became a quadriplegic (paralyzed limbs) after a horseback riding accident, they decided to address the issues related to a standard wheelchair. They have researched, designed, and engineered a customized wheelchair that addresses Sophia's main pain points and are now looking for ways to manufacture it.
Alan Esses and Alberto Esses - Boston
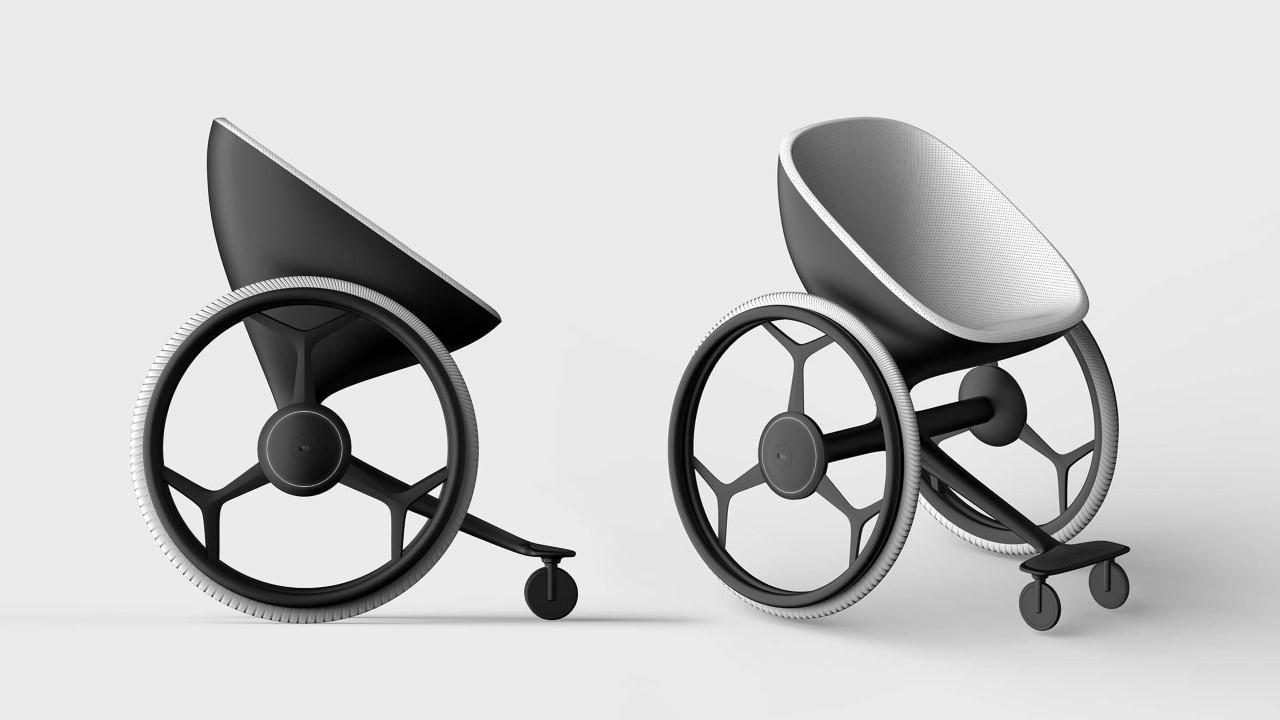
The Lunar Exploration Mechanical Arm from Concordia University Capstone Team
This project is centered around designing a robotic arm for implementation on a lunar rover that will be subject to the harsh environment of the lunar surface while having a limited energy supply. The team aims to develop a preliminary prototype and determine possible future directions.
The team is made up of seven undergraduate students from Concordia University in Montreal, Quebec. The Concordia team includes Aidan Mitchell, Eric Cappelli-Martell, Sean Le Noble, Erl Bernard, Joseph Corbisiero, Fady Mitry & Mustapha El Makdah.
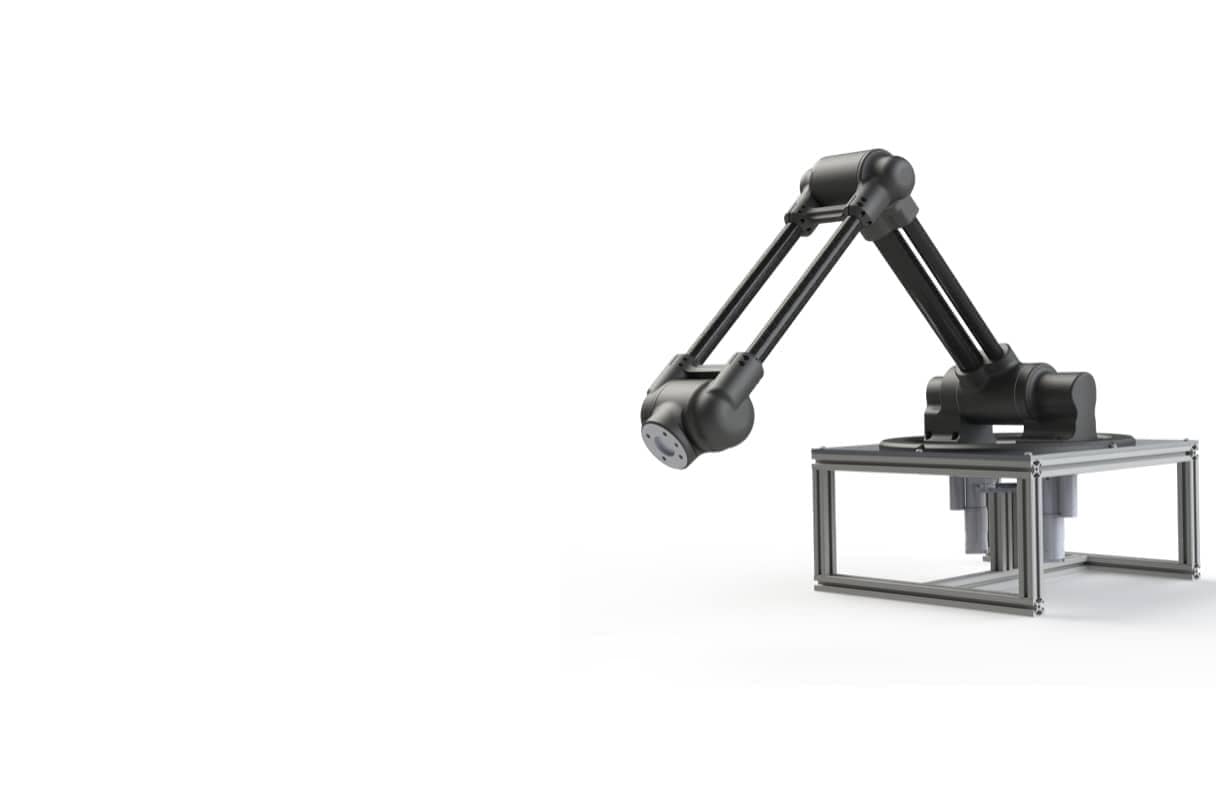
Our previous winners of the Engineering Challenges
KyronMAX® helps drones go Ultra-Quiet
An innovative take on 'ultra-quiet' unmanned aerial vehicle (UAV) blades. The novel blade design can help eliminate the incessant buzzing sound of drones, almost entirely. The patent-pending method used to mold the blades results in an average 10 dB sound reduction which is 50% quieter compared to equivalently sized conventional UAV propeller blades.
Delson Aeronautics

When something is holding you from participating
Are you unsure about your project? Do you think your project is too small? You don't know if your project fits into one of the programs? You have some unanswered questions?
Well don't hesitate and let's get in touch. We're here to help, guide and support you. Send your short message and indicate what fits you best : a call or a feedback mail or ..... just name it!